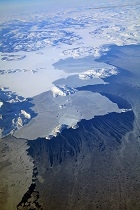
Arctic research and development (R&D) is fundamental to the safe and economic development of the region.
Companies are allocating funds to expand international knowledge about arctic conditions, improve the understanding of material behavior, advance analytical techniques, promote wider acceptance of progressive design philosophies, and implement reliable arctic operational strategies that will enable additional offshore arctic prospects to be developed.
With this backdrop, it is no surprise that research efforts are expanding in Newfoundland as the region works to enhance its reputation as a center of excellence for ocean technologies.
Partnering to advance research
In 2010, ABS, which has been pursuing arctic R&D initiatives for decades, established its Harsh Environment Technology Center (HETC) in St. John’s in partnership with Memorial University of Newfoundland (MUN).
The decision to locate the center in St. John’s was made with the recognition of the strength of the MUN faculty, the scope of opportunity for collaboration with companies and research entities in St John’s, and an overall climate that promotes research excellence.
The HETC is the cornerstone of ABS arctic research. With the goal of feeding back into its rules and guides, ABS supports fundamental ice mechanics research, largescale structures testing with loading application using ice, and the creation of advanced numerical simulation and analysis techniques.
Because safety often starts and stops with human interface, harsh-environment impacts on human behavior and the ability to function efficiently when protected from the elements are vital components of arctic research efforts.
The ABS team at HETC is engaged in the first phase of a joint industry project (JIP) focusing on ice loads on floating structures.
The work has facilitated informational exchange on subjects such as interaction scenarios, station-keeping systems, numerical models, and model testing procedures.
ABS has worked with industry experts to identify areas of uncertainty that will be explored to provide recommendations toward a dedicated full-scale measurement campaign.
HETC engineers also are supporting a project to quantitatively assess the effectiveness of physical ice management, a project that includes performance models of icebreakers in various ice conditions and under different tactical maneuvers.
In the interest of bringing the best minds to focus on arctic challenges, ABS organizes workshops that gather experts for collaboration on issues such as corrosion, and for discussing coatings requirements, including current International Maritime Organization Safety of Life at Sea regulations on the Performance Standard for Protective Coatings and the potential need for additional guidance.
A particular area of interest is how coatings might help reduce maintenance costs for assets operating in arctic conditions.
The arctic research team also is targeting winterization issues, using a risk-based approach that provides a way to comply with the intent of the ABS Guide for Vessels Intended to Operate in Low Temperature Environments in situations where it is impractical to meet certain prescriptive requirements.
This new systematic approach, which delivers a low level of risk while permitting the use of practical solutions, is being applied collaboratively with a designer to a new vessel design intended for harsh-environment operations. The project is providing valuable feedback that ABS will use to enhance the guide.
Technology advancements
INTECSEA, a company within the WorleyParsons Group, also is active in arctic research. The company is involved with a number of R&D projects managed by Petroleum Research Newfoundland and Labrador (PRNL), a not-for-profit organization that facilitates research and technology development on behalf of its members.
As a participant in the Arctic and Sub-Arctic Subsea Technology JIP, the company investigated conventional, enhanced, and active subsea production technologies. These included subsea separation, boosting, compression, direct electric heating, and power and controls, with the objective of compiling, expanding, and updating the state of the industry information.
An anticipated outcome of this project was better characterization of the relative nature of each emerging technology through evaluation of its application to several predefined notional field development scenarios.
Another harsh-environment JIP the company is active in focuses on the development of a trenching system for subsea pipelines, flowlines, and umbilicals in ice scour environments.
The goal of this JIP is to develop a full-scale, commercially ready burial/trenching system that can trench to depths greater than current industry norms in difficult and highly variable soil conditions in water depths to 300 m.
Results from this multi-phased project will enable future field developments to be planned based on a reliable, predictable trenching solution.
Pipeline risk was the subject of investigations carried out by C-CORE, a company that—with contributions from industry, research institutes, and consultants—led a comprehensive two-year R&D program called the Pipeline Ice Risk Assessment and Mitigation (PIRAM) to investigate pack ice scour risk to pipelines.
PIRAM’s objective was to develop engineering design tools to model the interaction of ice keels with the seabed, and through displacement of the seabed soil, estimate design forces on buried pipelines.
In the course of the project, methodologies were developed to determine contact frequency and loads from gouging ice keels, and pipeline mechanical behavior in response to ice keel load events was established.
This program led to engineering models and procedures that could be incorporated in industry best practices to mitigate risk and protect pipeline infrastructure from ice keel loading.
The program also identified the importance of multiple fingered keels. PIRAM’s contact frequency model established the interaction frequency between ice features and the seabed or subsea infrastructure, and the ice load model calculated the ice keel resistance for those interaction events.
Large-scale ice keel tests were a first of their kind, complementing work that included the investigation of the potential of ice limits—shape, resistance, and kinematics.
The pipeline protection model studied the interaction of ice features with pipeline systems. The models were integrated within an interactive graphical user interface to perform pipeline routing and burial analysis for protection against ice keel gouging, and a probabilistic pipeline burial analysis was incorporated that accounts for the influence of sub-gouge soil displacements.
Large pendulum experiments
While pipeline protection is vital, it also is important to protect floating units working in ice-infested areas.
Understanding the ice load capacity of arctic ships and offshore structures was one of the key aims of the C$7.2 million (US$6.6 million) Sustainable Technology for Polar Ships and Structures (STePS2) project at MUN.
In addition to the university, partners in this program include Husky Energy Inc., ABS, Samsung Heavy Industries Co. Ltd., Rolls-Royce Marine, and BMT Fleet Technology.
Government participants include the Atlantic Canada Opportunities Agency, and the Natural Sciences and Engineering Research Council of Canada, with the National Research Council Canada in the role of research partner.
After several years of design and construction, a special new test apparatus, called the large double pendulum, is housed in the structures lab at the Faculty of Engineering and Applied Science at Memorial University in St. John’s.
To date, the STePS2 team has carried out three ice impact tests by striking a one-meter diameter ice cone against a specially designed ice impact module, developed by Dr. Robert Gagnon, a physicist at the National Research Council of Canada’s Ocean, Coastal, and River Engineering facility in St. John’s.
The panel contains a high-spatial-resolution array of pressure sensors covered by a thin metal front face. The large ice cone and the impact module are mounted on swinging carriages weighing approximately 8,000 lb.
Before the test, the carriages are pulled back to a locked position. Upon simultaneous release, the carriages swing down, and the ice and impact module collide. Forces up to 300,000 lb. were measured in the early tests, with the carriages raised to approximately half of their range.
Depending on a number of factors, it might well be possible for the apparatus to produce impacts approaching 1 million lb. If the apparatus can produce impacts in the range of 600,000 lb., they will constitute the biggest ever performed in a laboratory.
When the tests on the impact module are complete, the next series of tests will measure ice impact on steel structural panels with the goal of determining the strength and overload capacity of ice class structures. Lab testing at full scale enables both realism and exact control of all test parameters.
Concrete abrasion
Surface abrasion due to ice contact can result in diminished integrity and increased loading for concrete structures in ice-infested waters.
The abrasion process often involves simultaneous perpendicular crushing along with the tangential sliding action of the ice mass across the surface of the concrete.
This grinding process can be observed in such structures as marine lighthouses. Few, if any, experiments modeling this dual-action process have been conducted or reported.
A series of experiments simulating this interaction process recently was carried out using the instrumented load frame at MUN.
Concrete beams were fabricated to simulate high-performance marine grades (70 MPa) used in offshore structures and a lower-performance standard grade (40 MPa) as a common benchmark.
The beams were affixed to the load frame so they could be translated horizontally while being impinged upon from below by an upward moving cone-shaped ice sample.
The research team executed several test runs under normal loads looking at crushing, combined crushing and sliding, and combined sliding and adhesion, carefully cleaning the concrete surface of ice and dust after each test.
The team used several cameras, among them thermal and high-speed cameras, to collect visual data from the concrete surface and ice cone.
Because the experiments were exploratory in nature, qualitative observations covering a wide range of mechanisms and outcomes were made, with the primary focus on concrete integrity and the mechanics of the ice contact/interface layer.
Researchers observed ice forces greater than 40 MT (88,000 lb.) in the normal direction under varying normal velocities and sliding velocities. There was noticeable concrete surface loss, attributable to the mechanisms of crushing, friction, and adhesion.
The surface temperatures of the ice trail on the concrete surface shortly after interaction were particularly remarkable as there were significant increments. Large vibrational forces and movements, possibly a result of stick-slip between ice and concrete, also were observed during the tests.
Because this experimental work is very recent, it would be premature to draw conclusions. However, the exploratory character of the test sequence was highly successful and indicates that it will be of significant practical value.
Improving vessel design
Ice-classed ship hull design has evolved to the point where a small amount of hull damage is considered acceptable. This is called “plastic” or “limit states” design.
In simple terms, this means that if an ice-classed ship’s hull experiences its full design load, it is expected to come away with a dent. This allowable permanent damage is not significant enough to impair the safety or operation of the ship.
This move to plastic or limit states design is a significant step toward more efficient, economical, and environmentally friendly ice-classed ships.
There is, however, an important “but.” Until recently, it was assumed that loads (like ice) that slide along the hull could be analyzed and designed for as if they did not move. In fact, this is the present state-ofthe- art in ship hull structural design.
This was true when the structural design point was elastic (that is, the full design load would not result in a permanent dent); however, research has uncovered that load movement along the hull invalidates this assumption when the load causes permanent damage.
In other words, as long as the load is simultaneously sliding along the hull and causing permanent damage, the hull’s ability to sustain the load is far less than if the load was not moving.
This was first discovered with numerical models and subsequently verified with a laboratory apparatus used to investigate this phenomenon.
This novel unit has been used to investigate moving rigid loads and moving ice loads causing various levels of permanent damage to steel plates and frames and has provided considerable insight into the behavior of both hull structures and ice during moving load events.
The results of this research will provide design methods for analyzing and designing ship structures for moving loads.
Focusing on efficiency and safety
For nearly 100 years, the National Research Council (NRC) has been known as a results-focused R&D performer, working with partners to provide innovation support, strategic research, and scientific and technical services.
The goal of NRC is to improve efficiency, safety, and security in the Arctic and to further sustainable resource development, marine safety technologies, and advancements in cold region infrastructure and transportation.
The next series of tests will measure ice impact on steel structural panels with the goal of determining the strength and overload capacity of ice class structures.
Proposed oil and gas exploration and production in the Arctic has inspired increased interest in the development of dynamically positioned (DP) drilling vessels capable of operating in pack ice.
Even in so-called managed ice conditions, where ice has been broken by support vessels, DP operations are challenging because of the extreme unpredictability and rapid variation of the ice load forces affecting the ship.
The goal of improving stationkeeping capabilities for both moored and DP arctic vessels has been the subject of NRC research for many years.
Recently, NRC signed an agreement to provide physical model test support and numerical model development for a C$8 million (US$7.3 million), five-year project led by the Centre for Marine Simulation at MUN.
As a partner in this initiative, NRC is helping to develop a simulation tool and related technologies for dynamic positioning of vessels in managed ice conditions with commercialization partner Kongsberg Maritime Simulations.
Funding partners include the Atlantic Canada Opportunities Agency, Petroleum Research Newfoundland and Labrador, and Research Development Corporation of Newfoundland and Labrador.
Comprehensive test facilities that contribute to finding solutions to complex problems such as these include a coastal wave basin (63 m x 14.2 m); a multidirectional wave basin (26 m x 36 m); various specialized flumes; cold test laboratories and thermal labs; the longest ice tank in the world (90 m x 12 m); and design and fabrication facilities for models and precision instrumentation.
Pushing boundaries
These programs are representative of the depth and breadth of R&D efforts in Atlantic Canada.
The projects described have borne fruit, and planned research efforts will continue to push back the boundaries of what is possible in arctic operations.
Many of these undertakings involve partnerships and draw on collaboration for both funding and human capital.
With great minds concentrating on the remaining challenges, progress is inevitable, and that progress will be much more rapid if these valuable resources are focused on the goal of discovering solutions together.
*Image credits: Flickr/Doc Searls Wikipedia
Post your comment
You cannot post comments until you have logged in.
Login to post a commentComments
No one has commented on this page yet.
RSS feed for comments on this page | RSS feed for all comments